En el mundo del nesting, trabajar con tubos puede ser muy diferente a hacerlo con chapas. Con la chapa, hay un nivel de libertad de Nesting que los fabricantes no tienen con el tubo. El Nesting suele ser más abierto y los talleres tienen la posibilidad de anidar a lo largo y ancho de la chapa, mientras que en el caso de los tubos, como sólo se trabaja en una dirección y la pieza ocupa la mayor parte del espacio, hay mucho menos margen de error. Los talleres tienen que mejorar mucho la optimización del Nesting de tubos, porque la más mínima diferencia en el orden o la orientación de las piezas puede arruinar su utilización.
Errores comunes
Desde una perspectiva de Nesting más general, no es raro que los fabricantes que trabajan con software de Nesting quieran intentar realizar un Nesting manual. En algunos casos, estos fabricantes creen que pueden hacer por sí solos lo que el software está diseñado para hacer. Aunque algunos tienen la perspicacia necesaria para crear un Nesting ajustado, pueden tardar horas en obtener resultados que el software de nesting podría determinar en cuestión de minutos.
Casi siempre, el software ofrece resultados tan buenos o mejores en una fracción del tiempo. Sin embargo, puede ser difícil romper con esa mentalidad manual. Con la llegada de una generación más joven al sector de la fabricación, es menos habitual ver esta dependencia del Nesting manual, tanto en el lado de las placas como en el de los tubos. Y tras realizar pruebas en paralelo, el software de Nesting demuestra su eficacia y versatilidad.
Cuando se trata de procesar tubos, muchos talleres no se dan cuenta de lo variada que puede ser la calidad del material. Cuando trabajan con máquinas manuales como sierras, la variabilidad del material es menos problemática. Pero cuando estos talleres pasan de trabajar con máquinas manuales a hacerlo con máquinas de corte CNC, esta variabilidad puede causar problemas.
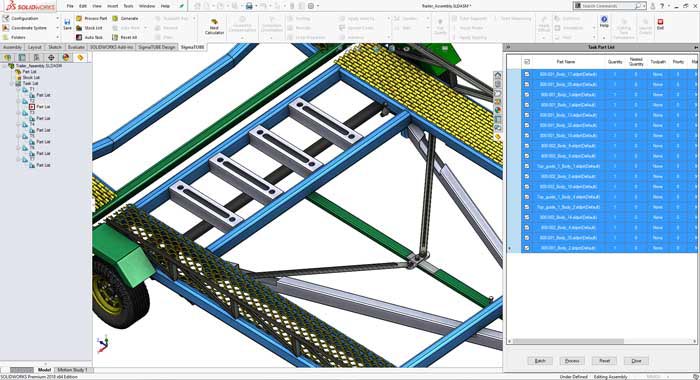
Una máquina CNC puede detectar incluso los cambios más pequeños en el material. Si la máquina no dispone de algo como el palpado para ajustar esa ligera diferencia de material, los fabricantes pueden encontrarse con piezas que tienen un aspecto un poco distinto del esperado, especialmente en comparación con las piezas cortadas manualmente. Es importante tener en cuenta la variabilidad del material siempre que sea posible.
El tubo rectangular presenta un reto adicional relacionado con la variabilidad del material. No es raro que el radio varíe en un tubo rectangular. Cuando se genera un programa basado en un tamaño o radio de material específico, la calidad del corte puede verse afectada si no se modifica el modelo CAD para reflejar con precisión el material real que se va a cortar.
Nesting para las capacidades de la máquina
Una de las primeras cosas que un taller debe tener en cuenta a la hora de optimizar el mecanizado de tubos es el anidado en función del tipo de máquina de corte con la que trabaje.
El Nesting puede servir para todo, desde una simple sierra que sólo hace cortes en los extremos hasta complejas máquinas láser con capacidades avanzadas de manipulación y carga/descarga de piezas. Sin embargo, las capacidades de anidamiento estarán directamente relacionadas con el tipo de máquina que se utilice.
En las sierras, el software de Nesting necesitará conocer parámetros específicos, como si va a cortar en paquetes. El software optimizará el Nesting para asegurarse de que la sierra puede cortar el mayor número posible de palos al mismo tiempo.
Con una máquina láser estándar, es importante entender que algunos de los sistemas de sujeción pueden dejar una zona muerta significativa en el palo. Por ejemplo, si los mandriles sujetan una longitud de 10 a 20 pulgadas en el extremo del tubo, la antorcha no podrá acceder a esta zona y, por tanto, no podrá cortarla.
En estos casos, algo como una función de Nesting en la zona muerta puede ayudar a maximizar el uso de material. Con esta función, los fabricantes suministran al software todas las piezas y éste las analiza para ver si alguna es lo suficientemente sencilla o larga como para colocarla en esta zona muerta, de modo que pueda utilizarse el extremo del palo. Mientras no haya características de corte, lo más probable es que se coloque en esta zona muerta.
En máquinas más avanzadas con sistemas complejos de carga de piezas y manipulación de materiales, también entran en juego los sistemas de sujeción. Por ejemplo, algunas máquinas de corte de tubos tienen cuatro grandes mandriles que son capaces de realizar toda la manipulación de material y existencias. Este tipo de máquina y sistema de sujeción puede cambiar de corte izquierda-derecha a corte derecha-izquierda cambiando los mandriles. El algoritmo del Nesting del software debe conocer estos procesos para aprovechar esta función de la máquina. Los fabricantes sólo tienen que indicar al motor de anidado la máquina con la que están trabajando y éste buscará todas las funciones y capacidades disponibles para aprovecharlas al máximo y anidar en consecuencia.

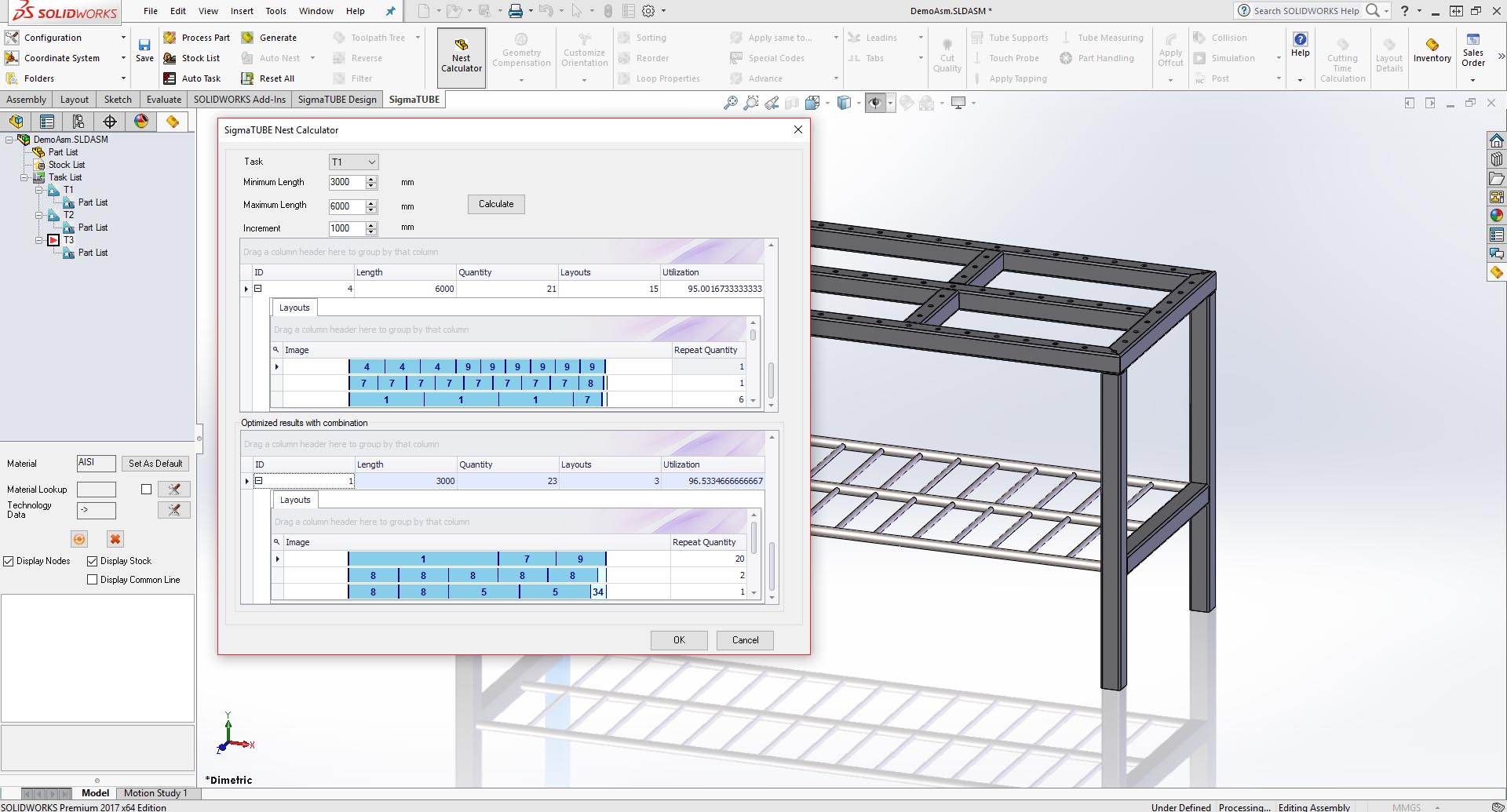
Nesting para la optimización de los materiales
La compatibilidad con el corte de línea común es una excelente forma de optimizar el uso de material. Sin embargo, es importante tener en cuenta que cuando se realiza Nesting 1D para máquinas tubulares, utilizar un corte de línea común en lugar de una distancia de corte puede ser la diferencia entre encajar una pieza más en el extremo.
En el caso de las máquinas de corte sin bisel, funciones como la compensación de 4 ejes pueden ser de gran ayuda para conseguir un ajuste correcto en el proceso de ensamblaje. Recortar el material sobrante en geometrías de inglete o copete utilizando esta función garantizará un ajuste bueno y limpio en el interior del tubo con cualquier componente al que se suelde en las fases posteriores.
En estos casos, el motor de Nesting puede consultar la trayectoria de la herramienta en lugar de la geometría real de la pieza en 3D para determinar lo cerca que pueden anidarse las piezas. Dado que la trayectoria de la herramienta dicta el aspecto que tendrá la pieza acabada, el software puede anidar un poco más cerca con esta función.
El Nesting puede servir para todo, desde una simple sierra que sólo hace cortes en los extremos hasta complejas máquinas láser con funciones avanzadas de manipulación y carga/descarga de piezas.
Nesting para la ejecución optimizada de programas
Para el procesado de tubos con máquinas láser, los fabricantes suelen trabajar con paquetes de la misma longitud de barra. La mayoría compran a un proveedor que suministra en dimensiones muy concretas; 240 pulg. es una de las más habituales.
Si un fabricante trabaja con la misma longitud de barra, el software de Nesting puede optimizar la creación de Nesting exactos en lugar de optimizar el material. Entonces, el motor examinará las piezas y calculará la mejor utilización de una barra y repetirá el programa una y otra vez.
Para los fabricantes que trabajan con diferentes longitudes de barras, es importante asegurarse de que el software permite optimizar la mejor combinación. Si el motor tiene dos longitudes diferentes, podrá determinar la mejor combinación de barras para una utilización óptima del material del almacén.
El Nesting también permite a los fabricantes especificar la longitud que desean utilizar. Por ejemplo, un taller puede especificar que el software utilice primero todas las longitudes más cortas para pasar por el mayor número posible de retales antes de pasar al inventario real de barras.
Crear Nestings que optimicen las tiradas del programa en lugar del material tiene sentido para los talleres que producen tiradas de lotes muy grandes, donde hay miles de piezas que cortar. Puede resultarles más beneficioso desde el punto de vista económico reducir el tiempo que un operario dedica a despegar y clasificar las distintas piezas, ya que los programas de anidado difieren mucho de un palo a otro.
Dado que no realizan muchas operaciones de descarga o de otro tipo, los talleres de bajo volumen/alta mezcla pueden aumentar todos los ajustes de optimización para garantizar que se maximiza la utilización del material. En estas aplicaciones tiene más sentido dar prioridad al material que a la optimización del programa.
Es importante que los fabricantes examinen los controles y vean qué es lo que mejor se adapta a las necesidades del taller. Por ejemplo, si un taller trabaja con grandes lotes, la máquina puede incluir funciones más avanzadas como la carga y descarga. En este caso, no importará que todos los programas sean diferentes porque la máquina es capaz de procesar rápidamente y ocupar el lugar del operario, liberándole para otras tareas. Un buen software de Nesting ofrece a los talleres la posibilidad de ajustar los diales y las optimizaciones como consideren oportuno.
El Nesting puede servir para todo, desde una simple sierra que sólo hace cortes en los extremos hasta complejas máquinas láser con funciones avanzadas de manipulación y carga/descarga de piezas.
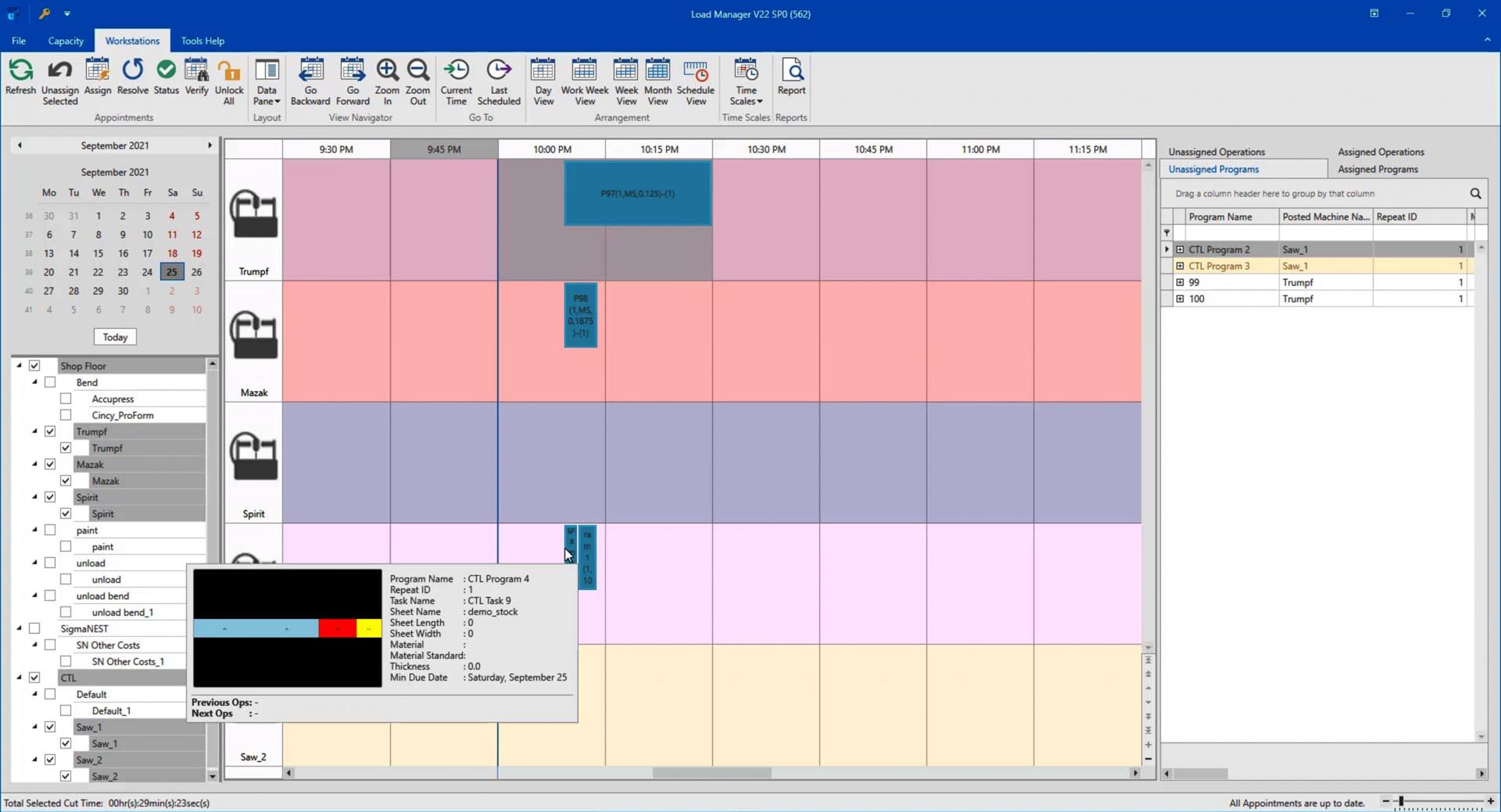
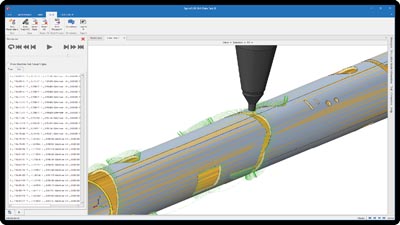
Calcular el tiempo y el coste
Una calculadora es otra buena herramienta para el mecanizado de tubos. Una de las principales ventajas es que la calculadora permite a los talleres introducir parámetros y determinar el tiempo y los costes sin tener que generar el programa para la máquina.
Los fabricantes pueden teclear todas las longitudes de tubos disponibles en el taller e incluso especificar con qué longitud empezar a trabajar. La calculadora del software de anidado tiene en cuenta todos los aspectos y determina el mejor proceso resultante en función de las longitudes de barra disponibles o incluso de las mejores longitudes de barra para un lote determinado.
Se trata de una función estupenda para presupuestar trabajos. Ofrece a los talleres la flexibilidad de ver si un trabajo merece la pena y combinar las longitudes de barra disponibles para optimizar el uso del material.
Publicado en Canadian Fabrication & Welding, febrero de 2022
"Tackling Tube Nesting" por Lindsay Luminoso, Redactora Asociada
https://www.canadianmetalworking-digital.com/february-2022/Tackling-Tube-Nesting
Entrevista con Dakota Baird, Product owner de tubo e importación de SigmaNEST