The Skeletal Integrity of a Moving Sheet
Following is part one of a larger article originally printed in the July 2019 issue of The Fabricator.
A fabricator usually invests in a punch/laser combination machine for one very compelling reason: to achieve more capabilities in one manufacturing step that doesn’t take up much floor space. A punch/laser machine can cut, form, and sometimes drill and tap all in one work envelope. Automated combo systems can denest and sort too. The machine can use punches for easy-to-punch geometries; form with form tools; laser-cut complex geometries; then denest and sort, all in one setup. It sounds like a panacea.
But there’s a learning curve too, and it’s a little different these days. Years ago many laser programmers started their careers on the punch press and then migrated to the laser. Now that laser cutting dominates, a laser programmer new to the combo machine must adapt to its idiosyncrasies.
Say you’re a top programmer in a shop where the cutting department uses lasers exclusively. Company leadership decides to invest in a punch/laser combination machine and makes you the lead programmer. Where do you start?
Advanced nesting software can account for many of the idiosyncrasies automatically. But as a programmer new to the punch/laser system, you might want to know why exactly the software is choosing to do what it does. You can also be sure that the final programs are the most stable and efficient they can be. The more you know, the better prepared you’ll be.
Part Orientation
On the laser, you can nest parts in any orientation. Sure, you might have restrictions dictated by business or job requirements, like putting certain grain restraints on parts. But the laser cutting machine itself has no restrictions on part orientation.
Not so with the punch/laser combo. You need to arrange certain parts on the nest to account for punch tools at fixed angles. Yes, you might incur a material yield penalty, but it’s probably a small price to pay if punching those parts is more efficient than laser cutting them, especially if the right punch shapes and (especially) form tools are available.
The Skeletal Integrity of a Moving Sheet
Because a laser cutting machine uses slats to support the material, you need to worry about parts falling into the slats and tipping up. You needn’t worry about this on a punch/laser combo machine, which usually supports the material with a solid roller table or brush table.
But you do need to worry about skeletal integrity during cutting, and it has to do with the way the material is handled during the cutting cycle. Most modern laser cutting machines are flying-optic systems in which the cutting head moves and the sheet remains stationary. Conversely, most punch/laser machines move the material during the cutting cycle.
X-Y Positioning
The combo system’s punch usually remains in the same X-Y position during operation while the sheet moves in X—just like a stand-alone punch press. When the combo system’s laser head cuts, depending on the machine, it moves slightly in X and Y, but the sheet itself does most of the moving—again, in the X direction. A gap below the beam allows heat to dissipate and molten metal to evacuate.
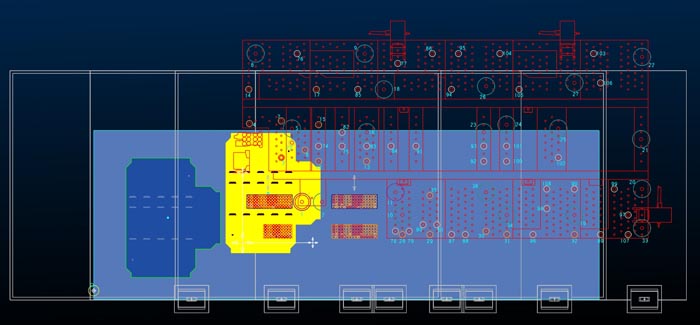
Because the sheet is moving, skeletal integrity matters. It can be affected by program sequence (covered later), part geometry, web width and the number of webs, as well as the material type and thickness. Generally speaking, thin, low-tensile materials have more problems with skeleton integrity than stronger and thicker materials.
Internal Stress
Another big factor is a material’s internal stresses. If you’re running, say, galvanneal with a lot of internal stress, cutting can release that stress and wreak havoc on process stability. Say a programmer creates a nest with many long, narrow parts, held in place by microjoints near the end of the program (again, because the sheet is moving). Cutting these long parts releases stress and causes them to bow upward, especially if they aren’t tabbed in the right places. That’s sometimes enough to crash into a processing head. Laser cutting programmers need to deal with this problem too, of course, but combo machine programmers must approach the problem differently because, again, the sheet is moving.
Common-line Cutting
A moving sheet—be it on a stand-alone punch or combo machine—also changes the rules for common-line cutting (CLC). From a business perspective, CLC looks compelling. After all, it’s designed to save time and material. That’s an enticing proposition.
On a punch or combo machine, you again need to consider the skeletal integrity of a moving sheet. If you common-line-cut a number of small parts together, all with a single web around them (like a big picture frame), you now have a big unsupported section with no integrity at all.
Another example: You have four octagons cut along a common line. On a laser, you’re left with a piece of floating scrap in the middle. If the scrap is large and stable enough so it won’t tip, it’s not a problem on a flatbed laser. But on a moving-sheet machine like a combo machine, you need a strategy to manage floating scrap and other unsupported material. Floating scrap is a safety hazard.
You’ll need to adjust your CLC strategy. You might cut with a common line only when it doesn’t leave floating scrap. Or you might perform CLC but with microtabbing to hold the parts and floating scrap in place. In fact, many small CLC parts could be tabbed together with the scrap and then lifted out with part removal automation or sent down a chute as one unit.
Schedule a demo to see how SigmaNEST addresses this and other Combo machine programming.